Classic Mini EFI #3 - Drive by Wire or Cable Driven throttle?
A comprehensive guide on the parts and basic concepts related to fuel injecting your Classic Mini. Diving deeper into the concepts of drive by wire vs cable-driven throttle bodies. Which to choose?
Which one should I choose?
The wild and wonderful world of fuel injected throttle bodies. Lets discuss a few different variants and why you may or may not what to pick one over another.
For the sake of this article we are making a few assumptions:
You are using an A-Series Engine
You are planning on sticking with a standard 5-port A-series head
You have an HIF44 intake manifold
You have not selected your ECU yet
Below are the two CMDIY throttle-bodies we produce and carry in house. You can see the primary differences between our two models. One with the built in Bosch motor for the throttle butterfly, while the other has your traditional throttle sweep and cable mount. Both run two injectors and roughly the same engine side flange. The only difference is the operation of the throttle butterfly.
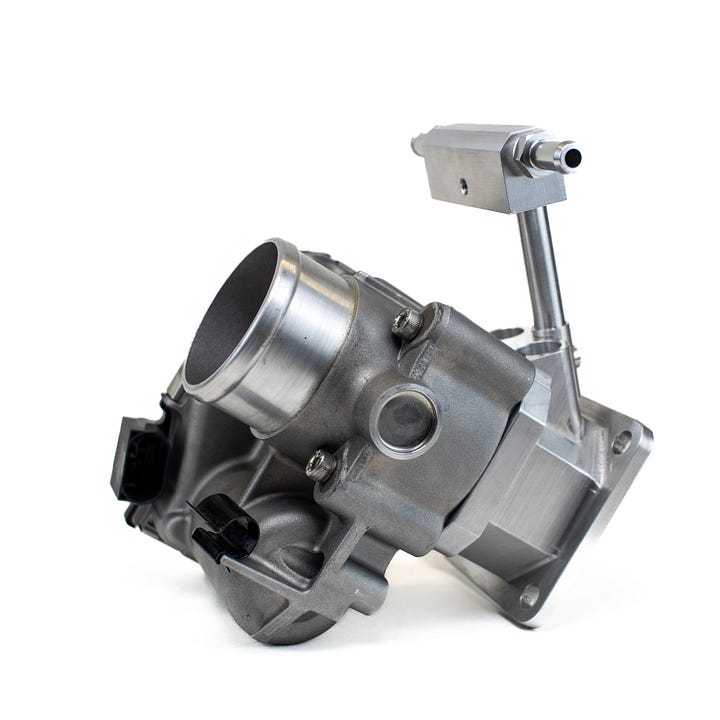

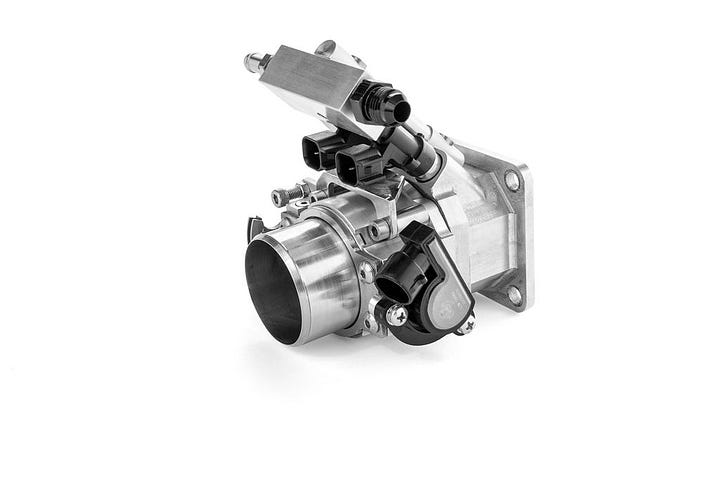
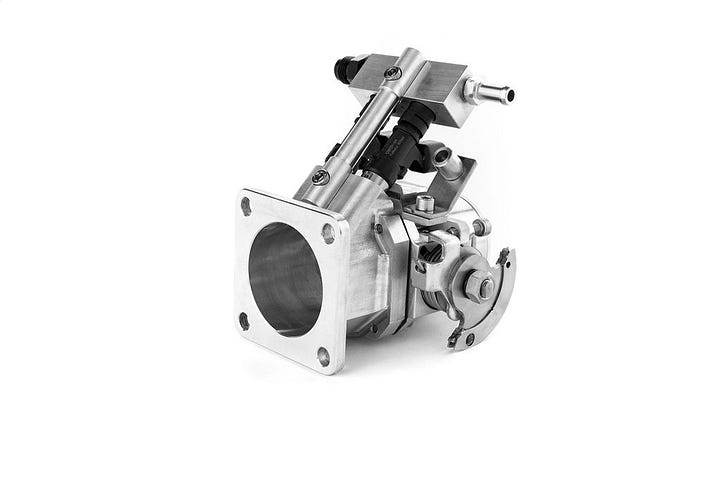
Deciding which option you want is more than just deciding which item to click buy on. The biggest deciding factor for your fueling choice is related to the ECU you plan to run, and what it can manage. However, the short answer is, if your ECU supports Drive by Wire (DBW), it is the clear and absolute best choice every time in my opinion. Although it appears more complex, drive by wire provides so much more reliability, control, and functionality over your traditional cable throttle setup. To help you decide whats right for you, lets break down the pros and cons.
Questions? Make sure to post a comment!
Cable EFI Throttle body:
Pros:
Works with just about any ECU on the market with largely no limitation in functionality.
Slightly less expensive up front costs
Less complex setup of wiring
More of a “Bolt-on” option as you can just run your existing throttle cable to the throttle body.
Comes with a variety of flanges (KN filter flange, tube flange, etc)
Cons:
Much harder to get a reliable idle than Drive by Wire (DBW)
Note: You can add an Idle Air Control Valve if your ECU supports it however this is added complexity
Cable is potentially a failure point
Objectively less safe when compared to DBW 1
Chance of stuck pedal
No throttle sensor redundancy
No safety cut outs
No brake pedal or clutch safety checks
Inability to implement custom throttle curves or have different driving modes
Cannot implement features like cruise control or valet mode
No ability to implement Launch Control
Drive by Wire Throttle body:
The throttle we use in our setups is a genuine Bosch motor attached to a 44mm throttle mouth. This is a serviceable and easily replaceable part used on many small bore OEM vehicles today. Namely most Fiat/Chrysler vehicles you drive past every day.
Pros:
Safer Operation2
Throttle Sensor Redundancy
No chance for stuck pedal
Configurable Safety cut out (ECU Dependent)
Brake and Clutch pedal Safety check (ECU Dependent)
Considerably more reliable with less points of mechanical failure
Dramatically better idle and cold start behavior
Ability to implement custom pedal curves
This allows custom configuration of how reactive you want your pedal
Launch Control (ECU Dependent)
Cruise Control (ECU Dependent)
Cons:
Not all ECU’s support Drive by Wire
Requires Drive by wire pedal or modified mini pedal
See Info below about DBW Pedal
More complexity in wiring at initial setup
Only available with hose attach flange
More expensive due to ECU required to operate
Drive by wire pedal
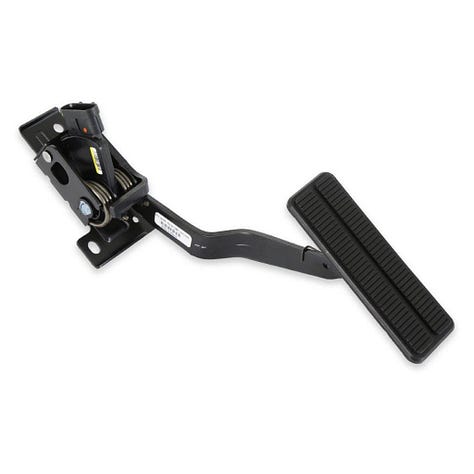
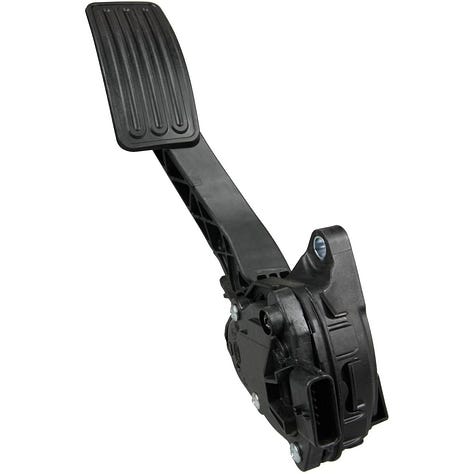

One of the drawbacks of the drive by wire setups is the requirement for a pedal sensor. This means either retrofitting your existing pedal to work with a pedal sensor or purchasing a bolt in pedal and replacing your existing one. In my setup I am running the retrofitted option modeled after a setup by Steve Blakemore or @turbocoopersport on Instagram. Essentially a small rose joint connecting the DSN Retrosport pedal to the Honda pedal sensor pictured above.
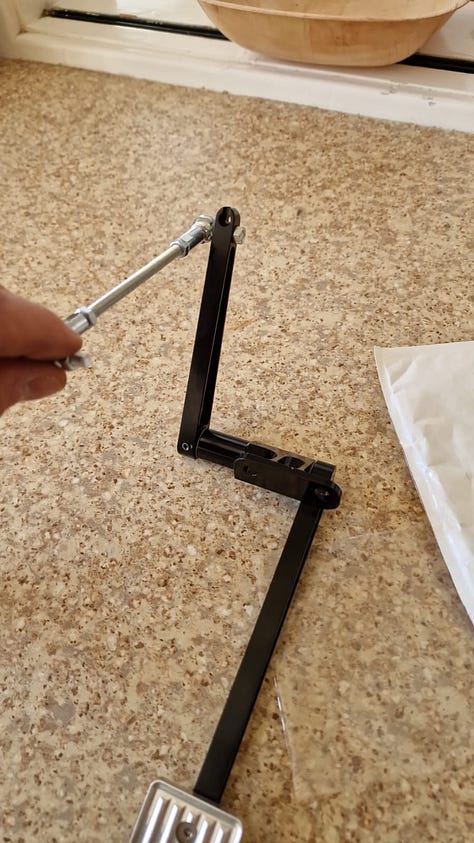


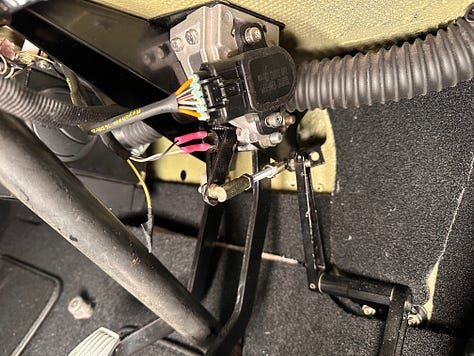

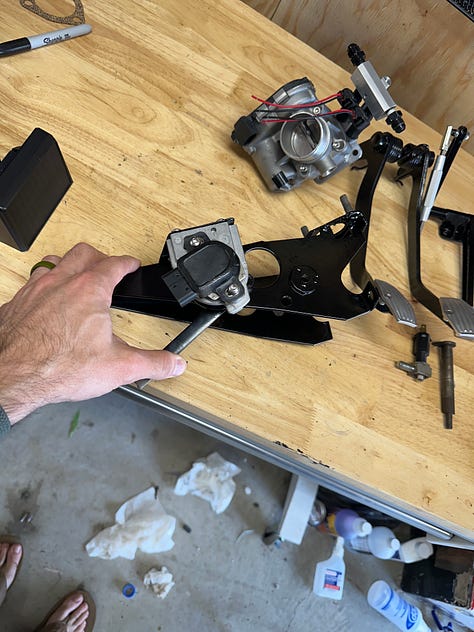
Conclusions
So between those two lists, there are always trade offs between the two systems however I feel the Drive by Wire system if you can accept the up front slightly harder setup, will reward you many times over when running your Mini and driving it day to day. If you need any more detail about the ECU’s you should choose or what each one supports, I have put together a small list below.
Side Note: Some Info about ECU’s
With the large variety of ECUs on the market, *Which ECU should I get? is the question I get asked the most. The short answer to this question is, "The one that offers you all the features you need for your setup". However, this answer is obviously not very helpful. So below I have put together a table of ECUs and the features they offer compared to what you may need for your setup. All the ECUs below will run an A-Series engine with varying degrees of complexity.
Some ECU’s you could use:
Haltech Elite 750
DBW - ❌
CMDIY Base Map - Purchase or Download
Haltech Elite 1500
DBW - ✅
CMDIY Base Map - Purchase or Download
Haltech Nexus R3
DBW - ✅
CMDIY Base Map - Purchase or Download
Emerald K6
DBW - ✅
CMDIY Base Map - Purchase or Download
Speeduino - DIY
DBW - ✅
CMDIY Base Map - Purchase or Download
MegaSquirt - DIY
DBW - ✅
CMDIY Base Map - Purchase or Download
Specialist Components (SCS) - Delta 4003
DBW - ❌
CMDIY Base Map - ❌
Specialist Components (SCS) - Delta 7004
DBW - ✅
CMDIY Base Map - ❌
Now this is not a comprehensive list of every ECU on the market. But these are the common ECUs I see people using in their Minis these days. My top pick for the Classic Mini owner is by far the Haltech Elite 1500 with Wiring Harness. This will sort out almost every EFI conversion I come across and they offer unparalleled support for their hardware via phone/email/chat.
A number of safety features are inherent in the design of OEM DBW systems. The APP sensor is required to have two position sensors, and the DBW throttle is also required to have two throttle position sensors (TPS). This requirement is so that the ECU can detect a malfunction in the sensor, and prevent it from commanding the DBW Throttle to a position other than that being sent from the APP. i.e. the throttle cannot open unexpectedly. There are multiple checks being monitored by the ECU to look for fault conditions, and in the event of a failure in the system the output to the DBW motor is cut. This will return the throttle to the rest position which is typically a fixed small amount of throttle opening. The amount of opening at rest is determined by the DBW throttle body design and not the ECU.
A number of safety features are inherent in the design of OEM DBW systems. The APP sensor is required to have two position sensors, and the DBW throttle is also required to have two throttle position sensors (TPS). This requirement is so that the ECU can detect a malfunction in the sensor, and prevent it from commanding the DBW Throttle to a position other than that being sent from the APP. i.e. the throttle cannot open unexpectedly. There are multiple checks being monitored by the ECU to look for fault conditions, and in the event of a failure in the system the output to the DBW motor is cut. This will return the throttle to the rest position which is typically a fixed small amount of throttle opening. The amount of opening at rest is determined by the DBW throttle body design and not the ECU.
Note that Specialist Components does not produce their own ECU and uses ECU’s produced by SCS. When looking for support on those kits I strongly recommend reaching out to SCS instead of Specialist Components.
Note that Specialist Components does not produce their own ECU and uses ECU’s produced by SCS. When looking for support on those kits I strongly recommend reaching out to SCS instead of Specialist Components.